At a Glance
After this project with Renoir, the client successfully yielded:
- An updated performance measurement system, including a field-based Activity Tracker, to capture data at the point of execution – to drive the continuous improvement process
- Benefits equating to at least a 5% FTE reduction
- In conjunction with the above project, an analysis of the Service Delivery function corrected for volume-based reductions yielded a further 12% FTE reduction
Background
The client is a government-owned electric power distribution company based in Asia Pacific that was founded in the 1920s and was later corporatised in the late 1990s. It has established itself as a multi-utility provider, supplying LPG and natural gas in addition to electricity, and has now expanded its operations into several new states.
The Challenge
The client’s key motivator was to develop and implement systems and processes to drive a reduction in rework and churn of planned work. The focus of the project was centered on its Service Delivery Division which was handling multiple complex projects. The goal was to reduce total workload, heighten productivity and identify any surplus of resources.
The context of these initiatives was to control commercial drivers, minimising project costs and complexity and improving delivery of projects on time and within budget.
What We Did
Analysis
The objective of this first phase of the Project was the handover of responsibilities from Asset Management to Design and Project Management. The programme was designed to develop and implement ‘fit for purpose’ processes and management control systems to provide a framework in which people could work efficiently and effectively across Business Operations, Network Programming, Project Design and Planning.
This was designed to reduce cycle times of processing work, which at the current volume levels would translate into a resource reduction ranged between USD 2.7M to USD 5.2M annualised, based on payroll expenditure equivalent to between 30 to 60 FTE.
The project focused on the transmission workstream – with solutions (and benefits) applied to the client’s distribution workstream. Studies were undertaken to identify the magnitude and nature of Churn and Rework. These studies included first person observations across all functional roles within scope, field-based data collection utilizing an Activity Tracker tool specially designed for this environment, and Management Control System analysis to identify process gaps.
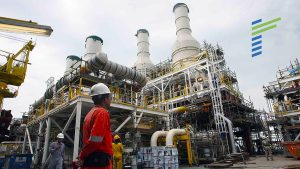
Oil & Gas Plant Optimizes Tool Time & Planning Efficiency
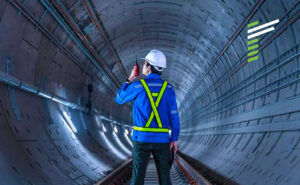
Clear KPIs and Communication Accelerate Construction Project
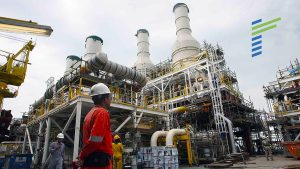
Oil & Gas Plant Optimizes Tool Time & Planning Efficiency
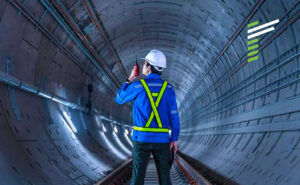
Clear KPIs and Communication Accelerate Construction Project
Implementation
All stakeholders were mapped for their communication needs spanning areas such as communication frequency, messages, and forums. Included in this communication strategy were key strategic messages to unions in line with the formal consultation processes in the Enterprise Agreement.
A SharePoint intranet site was also established to ensure access by all stakeholders. An online Activity Tracker was installed to measure Rework and deployment sessions were convened to bring together principle stakeholders to share relevant solutions and behaviour expectations.
This was further supported with one-on-one coaching provided by the project’s task force.
Project metrics were limited to the following:
- Rework reduction
- Overtime reduction
- Utilisation improvement
- Work order compliance
- Change request reduction
Results
The outcomes of the Delivery Enhancement Project were the formal management tools and working practices during handovers from Asset Management to Service Delivery that were developed. These tools formed the foundation for new ways of working to encourage continuous improvement. A few of these tools included the following:
- Short interval control via KPIs of planned activities to highlight and act on variances.
- Improved communications at interfaces.
- The client’s management team was trained in structured change management processes.
- A blueprint for operational processes and management control systems was developed as the standard way of working for the client.
- Improved single-point accountability
Reduce rework and churn with efficient management control systems.