At a Glance
- One of the Indonesia’s leading cellular providers partnered with Renoir to streamline its operations due to delays, bureaucracy and pressure from Indonesia’s telecom market.
- Through targeted improvements across supply chain, logistics, and network services, the client slashed delays by 67%, cut purchase orders by 90%, and boosted on-time deliveries by 250%.
- This case study highlights the impact of transformation that not only improved operational efficiency but also strengthened the company’s position in a highly competitive industry.
Key results
67% reduction
Supply chain management delays
90%
The number of purchase orders decreased
250%
Increase on On-time deliveries
Background
Indonesia’s telecom sector is highly interconnected, and at the client, SCM delays stalled material and equipment deliveries, causing project setbacks and cost overruns. These disruptions eroded operational efficiency, inflated expenses, and weakened competitive positioning in a fast-paced market. Bringing in Renoir for a full operational overhaul was vital, as the client’s legacy processes could no longer support its rapid network expansion and growing scale.
Analysis
The Indonesian telecommunications industry has become increasingly complex and fast-paced, requiring operators to respond with agility and operational efficiency. The client faced persistent challenges, including:
- A reactive approach to material requirement planning (MRP), hinders timely support for network growth
- Overly bureaucratic procurement processes with long service-level agreements (SLAs)
- Inefficient logistics are causing delays in material and equipment deliveries
- Rigid regional maintenance planning and unstandardized alarm management
- Weak coordination between headquarters and regional offices
- Outdated business processes are unable to support the rapid expansion of network demands
These inefficiencies limited the client’s ability to scale and maintain service excellence.
Project Approach
To address these challenges, Renoir Consulting was engaged to streamline and simplify several key business processes to achieve greater speed, predictability, and a lean execution approach. The project involved a time-specific assessment to understand the current state. Subsequently, three distinct projects were undertaken, focusing on procurement, logistics, network, and distribution processes.
- Supply Chain Group– Focused on procurement and logistics processes.
- Regional Operations – Targeted field operations and maintenance.
- Network Services – Addressed end-to-end site integration and network development.
Each project featured a structured management model with a Steering Committee comprising the client’s board and Management Action Teams led by department Vice Presidents. Renoir collaborated closely with General Managers and department heads to ensure seamless implementation.Â
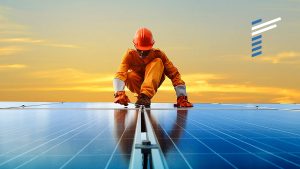
Management system drives efficiency and contractor compliance
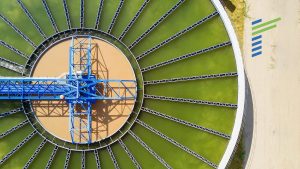
Reduce Operating Costs with Optimized Performance Management
Ready for a change in your organisation?
Implementation
Key initiatives executed in partnership with the client encompassed:
Supply Chain Group Project: Renoir introduced a new Management Control System to improve planning, oversight, and performance tracking in Procurement and Logistics. A standardised Bill of Materials (BOM) system was developed to streamline coordination between Engineering and Material Planning, while the Purchase Order (PO) process was simplified by removing redundancies and applying SLAs based on material criticality. Vendor and transporter performance was also closely monitored to improve delivery reliability.
Regional Operations:Â New SOPS for Preventive and Corrective Maintenance were co-created with engineers to enhance planning, formalise alarm prioritisation, and reduce response times. A Manpower Calculator Tool was also implemented to assess current and future resource needs accurately.
The Network Services Project: Optimised site integration processes by improving Site Acquisition, realigning priorities across Planning, Development, and Construction, and reducing bottlenecks. Enhancements at the Network Operations Centre (NOC) helped reduce customer complaints, while a new Network Coordination Group strengthened regional alignment and ensured consistent implementation of maintenance protocols.
“Renoir has been able to identify and help implement several improvements in the respective processes that have significantly helped the company strengthen its position in the market. We feel that Renoir has significantly contributed to the improved business performance over the last three quarters” Â
 – Chief Financial Officer
Results
The collaboration between Renoir and the client resulted in a significant transformation across key operational areas:
Supply Chain Management: Delays in material and equipment delivery dropped by 67% thanks to streamlined procurement and logistics systems. The PO process saw a dramatic 90% reduction, leading to faster approvals and execution.
On-Time Deliveries: The logistics team’s improved coordination and tracking boosted on-time deliveries by 250%, directly impacting project timelines and service reliability.
Network Services and Operations: The SOPs, manpower tools, and alignment mechanisms enhanced maintenance planning and execution. Site build times improved by 20–25%, and regional coordination improved through standardised communication protocols and newly established coordination groups.
This comprehensive transformation enabled the client to keep pace with its rapid network expansion while improving customer satisfaction and operational efficiency.
*Client-specific details have been intentionally omitted to maintain strict discretion.
Streamline key business processes and drive substantial gains in efficiency and productivity.