At a Glance
- A prominent academic medical centre faced issues including poorly managed point-of-care materials systems, inconsistent inventory management, departmental silos, and a lack of proactive strategic sourcing.
- Partnership with Renoir resulted in $13.1 Million, improved supply chain performance, the implementation of strategic sourcing principles, and a new organisational focus on continuous supply chain management.
- This case study connects the “how” with the “what” behind the herculean task of addressing client’s challenges within their supply chain management.
Key results
$13.1M
in savings from better sourcing, inventory, and pharmacy management
Purchasing became a proactive, strategic function
Cross-functional teamwork improved supply chain sustainability
Background
Hospitals manage a vast and complex inventory of medical supplies, equipment, pharmaceuticals, and consumables essential for patient care. Effective inventory management is critical to ensure the availability of necessary items, reduce costs, minimise waste, and prevent disruptions in patient care caused by stockouts or expired products.
However, factors such as unpredictable demand for certain drugs and equipment, the critical nature of timely availability, and the complexity of managing diverse product categories arise as challenges within this sector. Inventory shortages can lead to cancelled or rescheduled procedures, impacting patient outcomes. Therefore, advanced forecasting and integrated supply chain solutions are increasingly vital.
The client is a top-ranked academic medical centre in the United States, known for clinical excellence, innovation, and research. Despite its reputation and advancements in many areas, the hospital’s supply chain function lagged. With thousands of staff across various medical specialties and support departments, the organisation operated in silos that hindered efficient material flow and procurement optimisation.
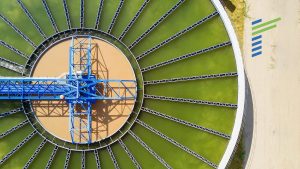
Reduce Operating Costs with Optimized Performance Management
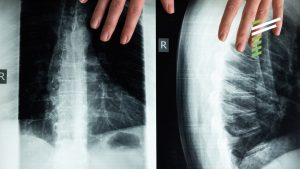
Vendor management saves healthcare centre $12 million
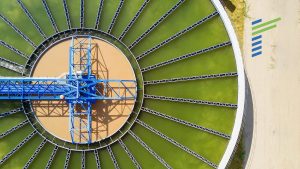
Reduce Operating Costs with Optimized Performance Management
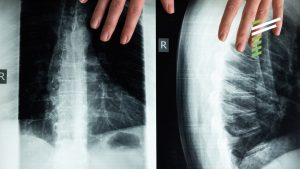
Vendor management saves healthcare centre $12 million
Ready for a change in your organisation?
Analysis
Renoir Consulting undertook a comprehensive analysis of the client’s supply chain activities across several key departments, including the operating rooms (ORs), sterile processing, Cardiology, Radiology, Materials, and Purchasing. The focus of this analysis was on understanding the existing process flows and management control systems and their impact on the efficacy of supply chain activities.
The analysis revealed several critical issues:
- The client’s point of care materials management system was not being correctly managed, leading to discrepancies between physical stock and system data and increasing the likelihood of stock-out situations.
- Inventory ‘days cover’ was not systematically reviewed, resulting in significant fluctuations between available and needed stock.
- Departmental silos existed in relation to supply chain management, hindering effective collaboration and optimisation. The Purchasing department primarily focused on order processing and lacked a proactive, value-adding approach. The concept of strategic sourcing was absent.
- The Materials Management department lacked strong relationships with its internal customers and was not perceived as a value-adding function.
Project Approach
Renoir initiated its Focus Process™ to engage stakeholders and establish alignment on the need for change. The approach included:
- Conducting detailed diagnostic analyses of key departments, including Operating Rooms (OR), Cardiology, Radiology, Sterile Processing, and Purchasing.
- Engaging cross-functional teams to co-develop solutions and improve ownership of supply chain processes.
- Emphasising the strategic value of supply chain as a driver for cost efficiency and operational excellence.
- Working closely with the client, Renoir facilitated the joint development of solutions to address the identified challenges.
Implementation
In partnership with the client, Renoir supported the implementation of several key initiatives to drive sustainable improvement:
Inventory Management System Enhancements: Significant improvements were made to the inventory systems associated with Materials Management. This included setting correct levels for inventory days cover and ensuring the point-of-care (Pyxis) system became more accurate.
Organisational Restructuring of Purchasing: The Purchasing department underwent a transformation, being reorganised into three key subgroups: Strategic Sourcing, Analysis & Support, and Transactional Purchasing. The recruitment of a Strategic Sourcing Director further reinforced this strategic shift. The focus moved towards value-adding activities related to strategic sourcing, while maintaining efficiency in transactional purchasing and cost control.
Improved Interdepartmental Communication: A crucial element of the implementation was fostering better communication between departments on supply chain issues. Multi-skilled groups were established during the engagement and continued beyond the project to sustain and further improve results. Horizontal processes were implemented across the entire medical centre to ensure smoother supply chain operations, leading to more savings opportunities and better tracking mechanisms.
Focus on Pharmacy Optimisation: Specific attention was given to the Pharmacy department, resulting in savings through addressing utilisation issues, converting branded medications to generics, and eliminating a bundled “risk sharing” agreement that was no longer deemed beneficial due to improved analytical capabilities.
Results
The partnership between Renoir and the client delivered a lasting and quantifiable impact:
- $13.1 million in savings were realised through pharmacy optimisation, strategic sourcing, and inventory improvements.
- A cultural shift occurred within the organisation, with supply chain management now viewed as a continuous improvement process rather than a back-office function.
- Purchasing was transformed from a transactional department into a strategic business partner, capable of driving long-term value.
- Inventory performance improved, reducing the risk of stockouts and creating a more reliable materials management process.
- Cross-functional teams and horizontal processes were institutionalised, enabling smoother supply chain operations and better alignment between clinical and non-clinical functions.
*Client-specific details have been intentionally omitted to maintain strict discretion.
Generate significant savings, increase operational reliability, and drive cultural change with targeted supply chain transformation.