At a Glance
- Achieving World Class Maintenance requires a set of metrics to track and guide improvement, as these metrics drive behaviour and provide insight into your organisation’s maintenance performance.
- Specific metrics vary from organisation to organisation, but key indicators of World Class Maintenance often include frequent and effective planned maintenance, high equipment productivity, consistent predictive maintenance compliance, and a comprehensive work order coverage percentage.
- The key to achieving world-class status lies in the application of suitable maintenance methods and techniques.
The adoption of World Class Maintenance (WCM), an integrated approach to streamlining asset maintenance practices, is critical to driving operational excellence within industrial organisations. WCM holds great promise for improving work processes that can be universally applied to improve the safety, economy and overall efficiency of assets, with studies suggesting productivity improvements of up to 20%. Â
The approach encompasses many techniques and tools such as Total Productive Maintenance (TPM) and Reliability-Centred Maintenance (RCM). It goes beyond siloed maintenance practices and focuses on using all available means to deliver exceptional value to customers. Â
Maintenance excellence, a hallmark of WCM, means that organisations have no maintenance problems while achieving the lowest maintenance costs, highest equipment reliability, and highest asset availability. Â
Metrics that matterÂ
Any form of improvement requires measurable metrics, and it takes a comprehensive set to achieve World Class Maintenance. Metrics matter because they drive behaviour. Having only one metric limits your people and can drive them into a corner, leading to unintended consequences. Â
To truly achieve WCM, your operational metrics should be among the best in your industry. The exact key performance indicators (KPIs) you track will be specific to your organisation, but may include frequent and effective planned maintenance, high equipment productivity, consistent and accurate compliance with predictive maintenance schedules, and a comprehensive percentage of work covered by a work order. Â
Steps to World Class Maintenance Â
Creating a World Class Maintenance (WCM) system is a challenging but rewarding exercise. To streamline this process and guide organisations towards achieving WCM excellence, this three-step process can be implemented:Â
1. Build the foundation
The first step in the WCM journey is to build a solid foundation by implementing the core maintenance processes. Once these basic functions are in place, opportunities for further improvement can be identified and addressed. At this stage, organisations should typically focus on efficiently managing inventory levels, establishing standardised work procedures, developing comprehensive plans and schedules for maintenance activities, and implementing computerised maintenance management systems (CMMS) to streamline maintenance processes and improve data management. Significant maintenance costs are incurred at this stage as the foundation is built.
2. Improving maintenance efficiency to reduce costs
The second stage of the WCM journey focuses on driving efficiency gains by minimising and eliminating equipment failure. This stage provides an opportunity for cost savings. Objectives include:
- Streamlining maintenance processes to improve performance
- Implementing strategies to minimise equipment failure
- Building internal capabilities to reduce reliance on external services
- Doing more with less through efficient work practices.
3. Maximising uptime and achieving WCM excellence
This is the pinnacle of WCM excellence. Organisations that reach this stage indicate that the organisation has successfully established itself as a world-class entity, setting the benchmark for maintenance excellence and operational reliability. Key indicators of success at this stage include:
- Assets operate at peak performance with minimal downtime
- Maintenance costs are minimised while maintaining high levels of reliability and asset integrity
- A culture of continuous improvement is embedded, driving ongoing optimisation of maintenance practices.
Methods and techniques for achieving world-class maintenance
In the quest for excellence in maintenance practices, a robust World Class Maintenance System (WMS) framework has emerged. Developed using Interpretive Structural Modelling (ISM), this framework encompasses a range of sub-functions, activities, and practices that are essential to achieving world-class maintenance performance.
The framework breaks down maintenance into critical sub-functions such as spare parts management, inventory and procurement, operational involvement, and others. WMS identifies all the relevant elements and their associated practices, paving the way for successful implementation.
Suitable methods are selected from (non-exhaustive list):
- Computerised Maintenance Management System (CMMS)
- Corrective Maintenance (CM)
- Preventive Maintenance (PM)
- Reliability-Centred Maintenance (RCM)
- Risk-Based Maintenance (RBM)
- Total Productive Maintenance (TPM)
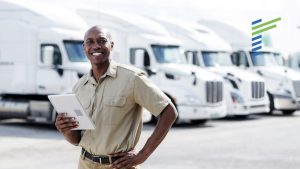
How to improve fleet efficiency for operational excellence
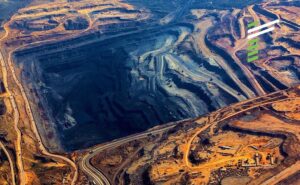
Charting a positive growth in the mining industry
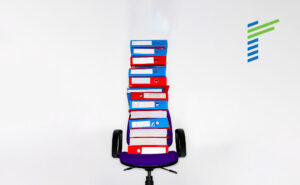
The productivity playbook for business success
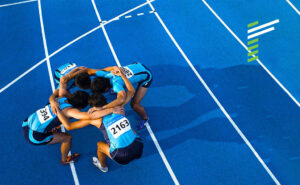
Winning business strategies from the world of sports
Ready for a change in your organisation?
The framework also provides a selection of techniques (non-exhaustive list), including:Â Â
- Root-cause analysis (RCA)Â
- Failure mode, effects, and criticality analysis (FMECA)Â
- Six SigmaÂ
- Pareto analysis (80/20 rule)Â
The key to achieving world-class status lies in the application of suitable maintenance methods and techniques.Â
Maintenance and reliability: Critical to success, now reshaped by data and analyticsÂ
Maintaining equipment and ensuring its reliability is critical for organisations across all industries. Proper investment in maintenance ensures reliable processes, which ultimately contributes to the success and sustainability of a business. Â
Today, maintenance and reliability is undergoing a significant transformation, driven by advances in technology, methodologies, and best practices. Data and analytics are now playing an important role in the transformation of this business area.  Â
Predictive maintenance, real-time condition monitoring, and machine learning/AI-based pattern recognition techniques are being used together with quantitative risk assessment to optimise both maintenance decisions and resource allocation. Â
With over 25 years of experience of implementing maintenance and reliability projects for companies in a wide range industry, Renoir is committed to delivering organisational and revenue outcomes by taking projects through to full adoption using our behavioural and cultural change methodologies. This approach ensures that your people and organisation can continue to add value long after the project has been delivered.Â
Improve the capability and reliability of your assets to maximise efficiency.